این مطلب از سایت دوست عزیزم . ( عمار قاسمیان عزیزی ) اقتباس شده است
Poly(phenylene oxide), or PPO, is one of those high-performance polymers we like to call engineering thermoplastics. Its biggest strength is its resistance to high temperatures. It has a very high glass transition temperature, 210 oC. But there"s a price for being heat-resistant. Most polymers are processed at high temperature in a liquid-like state. But if your polymer won"t become liquid-like at reasonable temperatures, you can"t process it! For this reason, PPO is often made into blends with high-impact polystyrene (HIPS for short). Blending PPO with HIPS makes the PPO easier to process, plus it gives PPO some resilience. PPO needs this toughening because by itself PPO can be brittle in some situations. General Electric makes PPO/HIPS blends and sells them under the name NorylTM.
Structurally, PPO is made of phenylene rings linked together by ether linkages in the 1,4 or para- positions, with a methyl group attached to carbon atoms in the 2 and 6 positions.
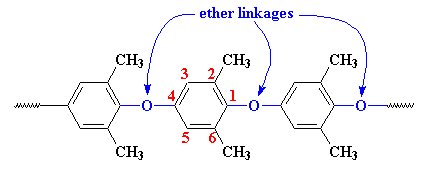
This polymer should really be called poly(2,6-dimethylphenylene oxide), but we call it poly(phenylene oxide) because we"re lazy.
PPO is made by what we call oxidative coupling polymerization of the monomer 2,6-dimethylphenol. Water is a by-product, and so this is a condensation polymerization.
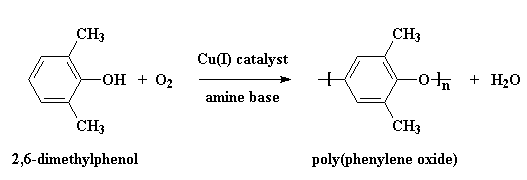
ترموپلاستیک الاستومر ها
Keywords
covalent bond, secondary interaction
We all know that elastomers are wonderful. Crosslinking makes this all possible. But crosslinked polymers can"t be recycled very easily. So in the interests of keeping the earth from becoming a giant landfill, we"ve come up with a new approach, the thermoplastic elastomer. The idea behind thermoplastic elastomers is the notion of a reversible crosslink.
Normal crosslinked polymers cannot be recycled because they don"t melt. They don"t melt because the crosslinks tie all the polymer chains together, making it impossible for the material to flow.
This is where the reversible crosslink comes in. Normal crosslinks are covalent, chemically bonding the polymer chains together into one molecule. The reversible crosslink uses noncovalent, or secondary interactions between the polymer chains to bind them together. These interaction include hydrogen bonding and ionic bonding.
The beauty of using noncovalent interactions to form crosslinks is that when the material is heated, the crosslinks are broken. This allows the material to be processed, and most importantly, recycled. When it cools again, the crosslinks reform.
Two approaches have been tried, ionomers and block copolymers.
Ionomers
Ionomers are a kind of copolymer. They are copolymers in which a small portion of the repeat units have ionic pendant groups attached to them. Not a lot, now, just a few. Normally the polymer backbone chain will be nonpolar. We all remember the rule, like dissolves like. It works here, too. The nonpolar polymer backbone chains will group together, and the polar ionic pendant groups will cluster together. Now as much as the cluster of ionic groups, snobbish as they are, would like to separate themselves completely from the nonpolar backbone chains, they can"t. Remember, they"re just sort of attached to the backbone chains. So what ends up happening is that these clusters of ionic groups serve to tie the backbone chains together, just like a normal crosslink would.
Except for one small difference. If we try, just for fun, to heat up these ionomers, something nifty and rather convenient happens. The ionic clusters will break up. When molecules get hot, they move around more. To be sure, this motion of molecules is heat itself. Moving around like this at high temperatures makes it hard for the ionic groups to stay put in their little clusters. So they break up. Now the ionomer has lost its crosslinks, and can be processed and recycled just like an ordinary polymer. Cool it back down, and the ionic clusters form again, and it acts like a crosslinked polymer again. Nifty, huh?
Block Copolymers
We can make a thermoplastic elastomer another way. That other way is called a block copolymer. A copolymer is a polymer made from more than one kind of monomer, that is, made out of two or more comonomers A block copolymer is a copolymer in which the comonomers are separated into long sections of the polymer backbone chain. Each of these sections, called blocks, looks sort of like a homopolymer.
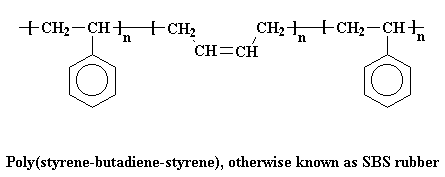
A very common thermoplastic elastomer that is a block copolymer is SBS rubber. SBS stands for styrene-butadiene-styrene, because SBS is made up of a short chain of polystyrene, followed by a long chain of polybutadiene, followed by another short chain of polystyrene. If we could stretch out a chain of SBS, it would look like the picture below.
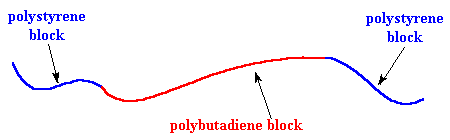
It"s time we let you folks in on a little secret: different polymers don"t mix very well. Remember the old "like dissolves like" rule? Well polymers are even more snobbish than small molecules. It"s very hard to mix two different polymers, even when they are very similar. This holds for the blocks of our SBS just as for any other polymers. So the polystyrene blocks tend to clump together and the polybutadiene blocks tend to clump together. The clusters formed by the polystyrene blocks tie the polybutadiene blocks together. Remember each polybutadiene block has a polystyrene block at each end, and the different polystyrene blocks of the same SBS molecule aren"t necessarily in the same cluster. This means that the different polystyrene clusters will be tied together by the polybutadiene blocks.
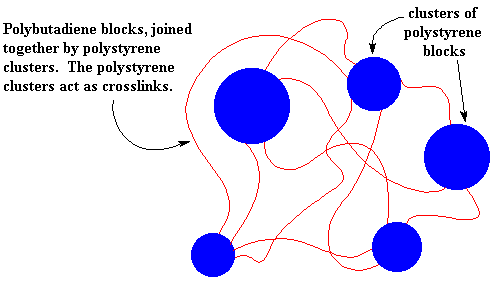
So the polystyrene clusters act as crosslinks for the polybutadiene blocks. And just like the ionic clusters of the ionomers, the polystyrene clusters break up when the SBS is heated, so it can be processed and recycled like a non-crosslinked polymer.
Being green seems to be easier than certain frogs thought!
But you can also make a thermoplastic elastomer using a block copolymer made form only one kind of monomer! I know that makes no sense, a copolymer with only one kind of monomer, but it"s true. You can make polypropylene in which there are blocks of different tacticity. One can make polypropylene with atactic blocks and isotactic blocks using metallocene catalysis polymerization, like this:
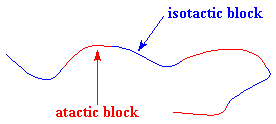
The blocks separate just as they do in SBS rubber. They separate because the isotactic blocks will form crystals, but the atactic blocks are amorphous. The result is something that looks like the picture you see on the right. It behaves as an elastomer for the same reasons as SBS rubber does.
Copyright ©2005 Polymer Science Learning Center Department of Polymer Science The University of Southern Mississippi